Green Steel: Revolutionizing Metal Manufacturing for a Sustainable Future
- Tectron Blogs
- Mar 1
- 2 min read
Updated: May 6
Steel is the backbone of modern civilization—used in everything from skyscrapers to household appliances. However, the traditional steelmaking process is resource-intensive, contributing significantly to global carbon emissions. Enter green steel, an innovative approach that has the potential to transform the industry while reducing its environmental impact.
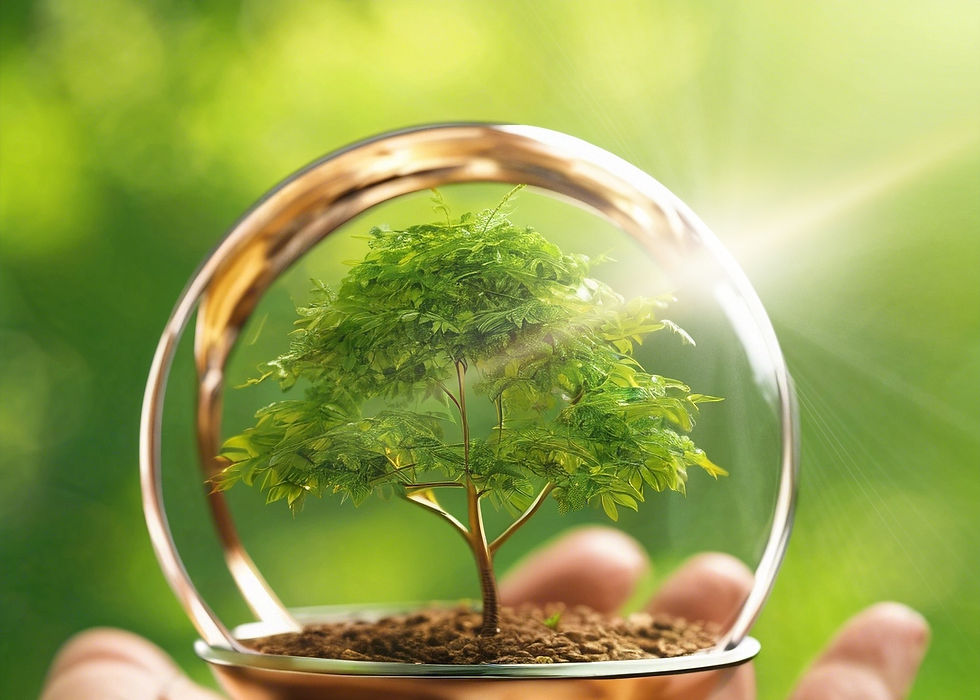
1. Understanding Green Steel
Green steel refers to steel produced using environmentally friendly processes aimed at reducing carbon emissions. This is achieved by substituting traditional fossil fuels—such as coal used in blast furnaces—with cleaner energy sources like hydrogen or renewable electricity.
Key Methods:
Hydrogen-based Direct Reduced Iron (H2-DRI): Replaces natural gas with green hydrogen in the iron reduction process.
Electric Arc Furnaces (EAF): Utilizes recycled scrap steel and renewable electricity.
2. The Environmental Impact of Traditional Steelmaking
Traditional steel production accounts for approximately 7-9% of global greenhouse gas emissions. This stems from:
Dependence on coal in blast furnaces.
High energy consumption in processing and refining.
Emissions during ore extraction and transportation.

3. Innovations Driving the Green Steel Movement
Recent innovations are making green steel viable, including:
Electrolysis Technology: Producing iron ore with minimal emissions.
Renewable Energy Integration: Transitioning plants to solar, wind, or hydropower sources.
CCUS (Carbon Capture, Utilization, and Storage): Capturing emissions from traditional plants and reusing or storing them.
4. Challenges to Overcome
While promising, green steel isn't without its challenges:
Higher Initial Costs: Implementing hydrogen-based processes and renewable infrastructure requires significant investment.
Energy Demand: Hydrogen production and electric arc furnaces rely heavily on consistent renewable energy supply.
Market Competition: Traditional steel still dominates the market due to lower costs.
5. Why Green Steel Matters
The push for sustainability is no longer optional. Companies and nations worldwide are setting ambitious carbon neutrality targets. Green steel contributes by:
Significantly lowering industrial emissions.
Aligning with ESG (Environmental, Social, and Governance) standards.
Future-proofing the industry against stricter environmental regulations.

6. Case Studies: Pioneers of Green Steel
Several companies are taking the lead in green steel production:
Hybrit (Sweden): Utilizing hydrogen-based processes, Hybrit produced the world’s first green steel, with plans to scale by 2030.
SSAB: Partnering with Hybrit and Volvo to introduce fossil-free steel in automotive manufacturing.
ArcelorMittal: Investing in renewable energy-powered steel plants and carbon capture technology.
7. The Future of Steel Manufacturing
As technology advances and renewable energy becomes more accessible, green steel could become the industry standard. Governments, investors, and consumers will play a crucial role in supporting this transition.
8. Call to Action
The journey toward green steel requires collaboration across industries, policymakers, and consumers. Metal manufacturers can start by:
Investing in research and development of sustainable technologies.
Adopting renewable energy sources.
Educating stakeholders on the long-term benefits of green steel.
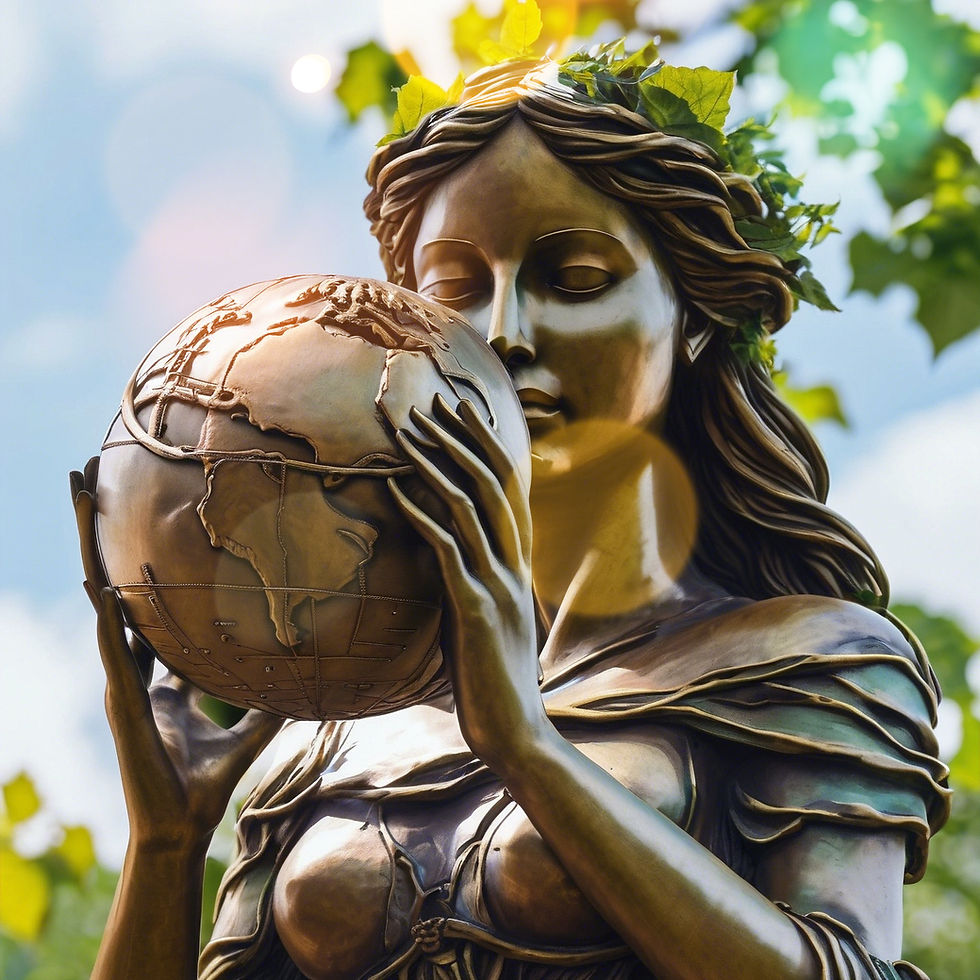