Hydraulic Press Brakes vs. Electric Press Brakes: A Performance Showdown
- Tectron Blogs
- Feb 24
- 3 min read
Updated: May 6
In the realm of metal fabrication, the press brake stands as a cornerstone, shaping raw materials into intricate components. Two dominant technologies vie for supremacy: hydraulic and electric press brakes. While both achieve the fundamental task of bending metal, their underlying mechanisms, performance characteristics, and ideal applications diverge significantly. Understanding these differences is crucial for manufacturers seeking to optimize their operations and investments.
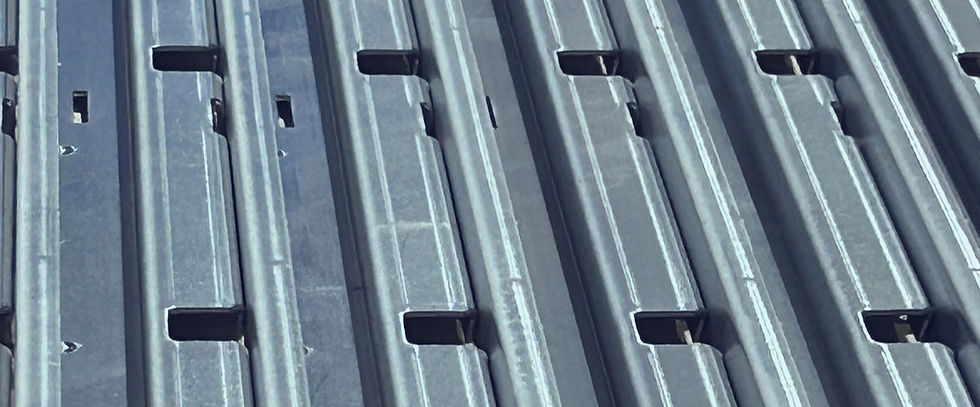
Hydraulic Press Brakes: The Powerhouse of Tradition
Hydraulic press brakes, the veterans of the industry, rely on hydraulic fluid to generate the immense force required for bending thick and heavy materials. They employ a system of pumps, valves, and cylinders to control the movement of the upper beam (ram), delivering consistent and powerful bending across the entire working length.
Strengths of Hydraulic Press Brakes:
High Force Capacity: Hydraulic systems excel in generating substantial force, making them ideal for handling thick materials and complex bends. They are the preferred choice for heavy-duty applications demanding high tonnage.
Long Stroke Length: Hydraulic press brakes typically offer longer stroke lengths, allowing for the formation of deeper bends and more intricate shapes.
Cost-Effectiveness (for High Tonnage): When dealing with applications requiring very high tonnage, hydraulic systems tend to be more cost-effective compared to their electric counterparts.
Durability: With proper maintenance, hydraulic press brakes are known for their longevity and robustness, capable of withstanding demanding workloads.
Weaknesses of Hydraulic Press Brakes:
Lower Precision: Compared to electric press brakes, hydraulic systems can exhibit slightly lower precision due to variations in hydraulic fluid temperature and valve response times.
Higher Energy Consumption: Hydraulic pumps consume significant energy, contributing to higher operating costs.
Maintenance Requirements: Hydraulic systems require regular maintenance, including fluid changes, filter replacements, and seal inspections, to prevent leaks and ensure optimal performance.
Environmental Concerns: Hydraulic fluid leaks can pose environmental risks, necessitating careful handling and disposal.
Slower Operation: in general, hydraulic presses can be slower than electric presses, especially in regards to repeatability, and speed of motion.
Electric Press Brakes: The Precision Performer
Electric press brakes, the modern contenders, utilize servo-electric motors to drive the ram, eliminating the need for hydraulic fluid. They offer superior precision, speed, and energy efficiency, making them well-suited for applications demanding tight tolerances and high production volumes.
Strengths of Electric Press Brakes:
Superior Precision and Accuracy: Servo-electric motors provide precise control over the ram movement, resulting in exceptional bending accuracy and repeatability.
Higher Speed and Productivity: Electric press brakes offer faster ram speeds and shorter cycle times, leading to increased productivity and throughput.
Energy Efficiency: By eliminating hydraulic pumps and valves, electric press brakes significantly reduce energy consumption, lowering operating costs.
Reduced Maintenance: Electric systems require minimal maintenance, reducing downtime and associated costs.
Environmental Friendliness: The absence of hydraulic fluid eliminates the risk of leaks and associated environmental hazards.
Quieter Operation: Electric machines generally operate much quieter than hydraulic machines.
Weaknesses of Electric Press Brakes:
Higher Initial Cost: Electric press brakes typically have a higher initial purchase price compared to hydraulic models.
Limited Force Capacity: While electric technology is continually advancing, electric press brakes generally have limitations regarding total achievable force, and tonnage, in comparison to large hydraulic presses.
Stroke length limitations: Generally electric press brakes, also have limitations on their stroke length.
The Performance Showdown: Key Considerations
The choice between hydraulic and electric press brakes hinges on several factors, including:
Application Requirements:
For heavy-duty applications involving thick materials and high tonnage, hydraulic press brakes remain the stalwart.
For precision bending, high-speed production, and energy efficiency, electric press brakes are the clear winners.
Budget:
Consider both the initial purchase price and long-term operating costs, including energy consumption and maintenance.
Production Volume:
Electric press brakes excel in high-volume production environments demanding fast cycle times.
Environmental Concerns:
If environmental sustainability is a priority, electric press brakes offer a greener alternative.
Operator Skill Level:
Electric press brakes with advanced CNC controls, can, in some cases, simplify operations.
Conclusion
Both hydraulic and electric press brakes play vital roles in modern metal fabrication. Hydraulic press brakes deliver brute force and reliability for heavy-duty applications, while electric press brakes offer precision, speed, and efficiency for high-volume production. The optimal choice depends on the specific needs and priorities of each manufacturer. By carefully evaluating the performance characteristics and cost considerations, manufacturers can select the press brake technology that best aligns with their operational goals.