TIG vs. MIG Welding: Understanding the Pros and Cons for Different Metals
- Adriana Gutierrez, Digital Media Producer
- Feb 27
- 2 min read
Updated: May 6
Welding, a critical process in metal fabrication, offers various techniques, each suited for specific materials and applications. Among the most popular are Tungsten Inert Gas (TIG) welding and Metal Inert Gas (MIG) welding. While both utilize shielding gas to protect the weld, their methods and results differ significantly. This article dives into the pros and cons of TIG and MIG welding, focusing on their suitability for different metals.
MIG Welding: Speed and Efficiency
MIG (Metal Inert Gas) welding, also known as Gas Metal Arc Welding (GMAW), uses a continuously fed wire electrode that melts and joins the base metals. It's known for its speed and ease of use, making it popular for production environments.
Pros of MIG Welding:
High Speed: MIG welding is faster than TIG, making it ideal for high-volume production.
Ease of Use: It's relatively easy to learn, requiring less operator skill.
Versatility: Suitable for a wide range of metals, including steel, aluminum, and stainless steel.
Continuous Wire Feed: Allows for long, uninterrupted welds.
Cost-Effective: Often more cost-effective for larger projects.
Cons of MIG Welding:
Lower Precision: Not as precise as TIG, leading to less aesthetic welds.
More Spatter: Produces more spatter, requiring post-weld cleanup.
Less Control: Offers less control over the heat input and weld puddle.
Not Ideal for Thin Metals: Can be challenging to use on very thin materials.
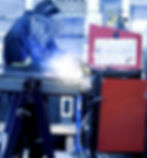
TIG Welding: Precision and Quality
TIG (Tungsten Inert Gas) welding, also known as Gas Tungsten Arc Welding (GTAW), uses a non-consumable tungsten electrode to create the arc. It offers exceptional precision and control, resulting in high-quality welds.
Pros of TIG Welding:
High Precision: Provides excellent control over the heat input and weld puddle.
High-Quality Welds: Produces clean, aesthetically pleasing welds with minimal spatter.
Versatility: Suitable for a wide range of metals, including aluminum, stainless steel, and titanium.
Ideal for Thin Metals: Excellent for welding thin materials.
No Spatter: Produces very little to no spatter.
Cons of TIG Welding:
Slower Speed: Slower than MIG, making it less efficient for high-volume production.
Higher Skill Level: Requires a higher level of operator skill.
More Complex Setup: More complex setup and operation.
Higher Cost: Generally more expensive than MIG welding.
Metal Suitability:
Steel:
MIG: Excellent for general steel fabrication due to its speed and efficiency.
TIG: Suitable for high-quality welds and thin steel applications.
Aluminum:
MIG: Can be used, but requires specialized equipment and techniques.
TIG: Preferred for aluminum due to its precision and control.
Stainless Steel:
MIG: Suitable for general stainless steel fabrication.
TIG: Preferred for high-quality, corrosion-resistant welds.
Titanium:
TIG: The preferred method due to its precision and control.
Choosing the Right Method:
The choice between TIG and MIG welding depends on the specific needs of the project.
Choose MIG when:
Speed and efficiency are crucial.
High-volume production is required.
General fabrication of steel is the primary task.
Choose TIG when:
High precision and quality are essential.
Thin materials are being welded.
Welding aluminum, titanium, or high-quality stainless steel.
Conclusion:
Understanding the pros and cons of TIG and MIG welding is crucial for selecting the appropriate technique for different metals and applications. MIG welding offers speed and efficiency for general fabrication, while TIG welding provides precision and quality for specialized applications.